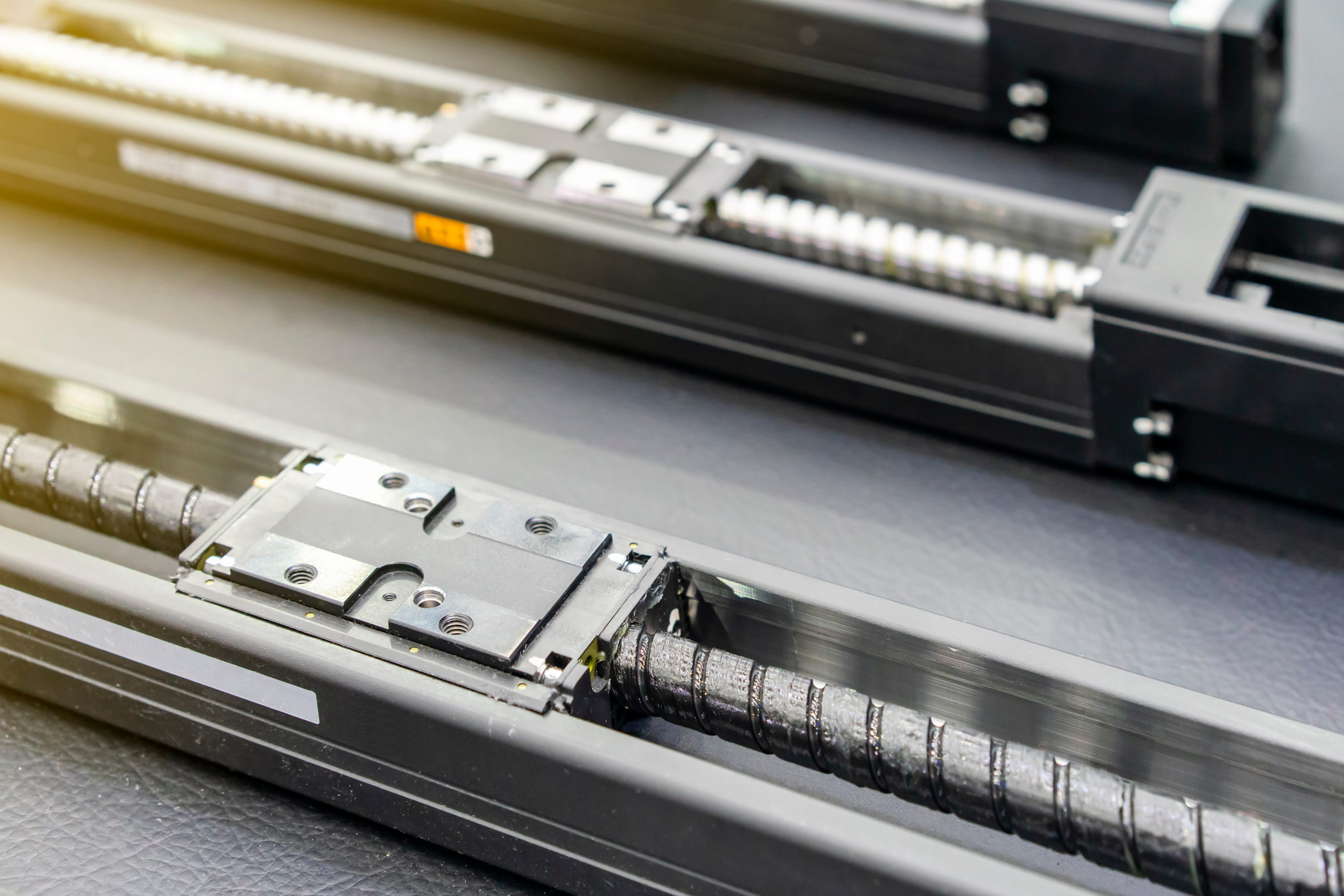
Motors
Home » Products » Motors
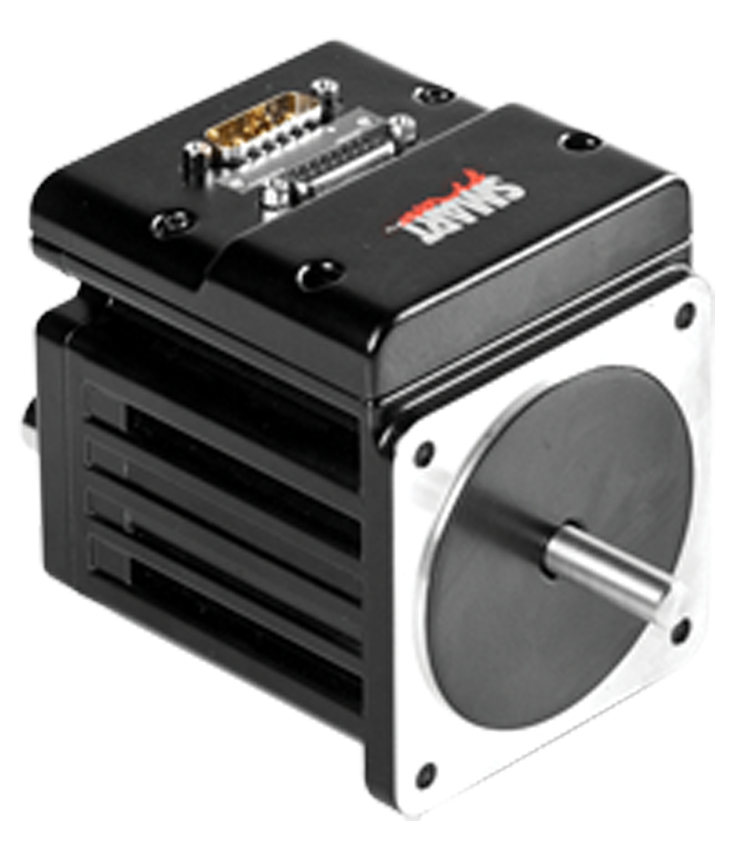
Motors are essential component for any motion control system. It’s role in the system is to convert electrical energy into mechanical motion. The choice of motor type depends on factors like speed, torque, inertia and repeatability of which are driven by the applications needs and requirements. When selecting a motor, it is important to review these parameters to determine which motor and what accessories are needed for a successful application.
How to Size a Motor?
- Speed: Speed refers to the rotational velocity of the motor shaft. Determine the desired operating speed for your application. Consider factors such as production cycle time, conveyor speed, or any other specific requirements related to motion speed.
- Torque: Torque is the tendency of a force to rotate an object around an axis. In the context of motors, it represents the twisting force required to move a load. To size a motor, calculate the required torque based on the load characteristics and desired acceleration or deceleration rates.
- Inertia: Load inertia (often denoted as “J”) is the resistance of an object to changes in its rotational speed. It depends on the mass distribution and geometry of the load. Calculate the total inertia by considering both the motor rotor inertia and the reflected load inertia (if geared). In an ideal system, the inertia of the load will not be greater than 10x the inertia of the motor. When there is a large load/mass involved we use mechanical advantage (gearing) to achieve a 10:1 ratio of load inertia to motor inertia.
- Controls: The control system plays a crucial role in motor sizing. Consider whether you need open-loop control (such as with stepper motors) or closed-loop control (using servo motors). Closed-loop systems can handle larger inertia ratios than open-loop systems.
Types of Motors:
- DC Brushed Motors:
- Description: DC brushed motors use wound coils of wire to create a magnetic field. The rotor (the part that rotates) contains these coils, which are free to rotate. The stator (the fixed part) houses permanent magnets that provide a stationary magnetic field.
- Commutation: In brushed motors, commutation (switching the current flow in the coils) is achieved mechanically using brushes and a commutator. As the rotor turns, different sets of rotor windings are switched on and off, causing the rotor to spin.
- Brushless DC (BLDC) Motors:
- Description: Brushless motors replace the mechanical commutation function with electronic control. They use permanent magnets on the rotor and electronic circuitry to switch the current in the stator windings.
- Commutation: BLDC motors use electronic sensors (Hall effect sensors) or sensorless techniques to determine the rotor position and control the current flow. This eliminates the need for brushes and commutators.
- Stepper Motors:
- Description: Stepper motors are a type of brushless DC motor with a specific coil arrangement that achieves a fixed number of stops or detents, subdividing the full circle of rotation.
- Working Principle: Stepper motors have evenly spaced windings in the stator that act as magnetic poles when powered. The rotor consists of permanent magnet pairs.
- AC Motors:
- Description: AC motors operate on alternating current and come in various types (e.g., induction motors, synchronous motors).
- Working Principle: AC motors use magnetic fields generated by alternating current to induce rotation.
If you have an application that requires a motor, please reach out to one of our industry experts; they will work with you to determine the ke performance attributes for your application and then work you to size/select the best solution for your application.
Moog Animatics – SmartMotors A Complete Motion Control System inside the SmartMotor™ What makes the Moog Animatics SmartMotor™ by far the most powerful integrated motor in the industry is its unique ability to control an entire machine. The SmartMotor is …
LinMot – Linear Motors LinMot motors are high quality, extremely high efficiency tubular linear motors. This high efficiency means less heat generated and better position accuracy. The simple, clean tubular design makes it easy to install the motor, reducing the …
The Class 5 SmartMotor™ is a highly programmable, fully integrated servo motor system that incorporates a motor, an encoder, an amplifier, a controller, serial communication, and IOs in one compact package. All D-style SmartMotor™ have a primary RS-232 communications port, …
Animatics – Class 5 M Style The Class 5 SmartMotor™ is a highly programmable, fully integrated servo motor system that incorporates a motor, an encoder, an amplifier, a controller, serial communication, and IOs in one compact package. They also feature …
The Animatics Class 6 D-Style SmartMotors deliver high performance and precision in a compact package. These motors integrate a motor, amplifier, controller, and multi-turn absolute encoder into a single unit. This integration provides a seamless solution for various industrial applications. With a …
Animatics – Class 6 M Style The Class 6 M-Style SmartMotor lineup includes EtherCAT® (EEC option), PROFINET® (EPN option), and EtherNet/IP™ (EIP option) versions. These motors are designed for maximum performance and connectivity. They incorporate a high-end, high-speed processor for …