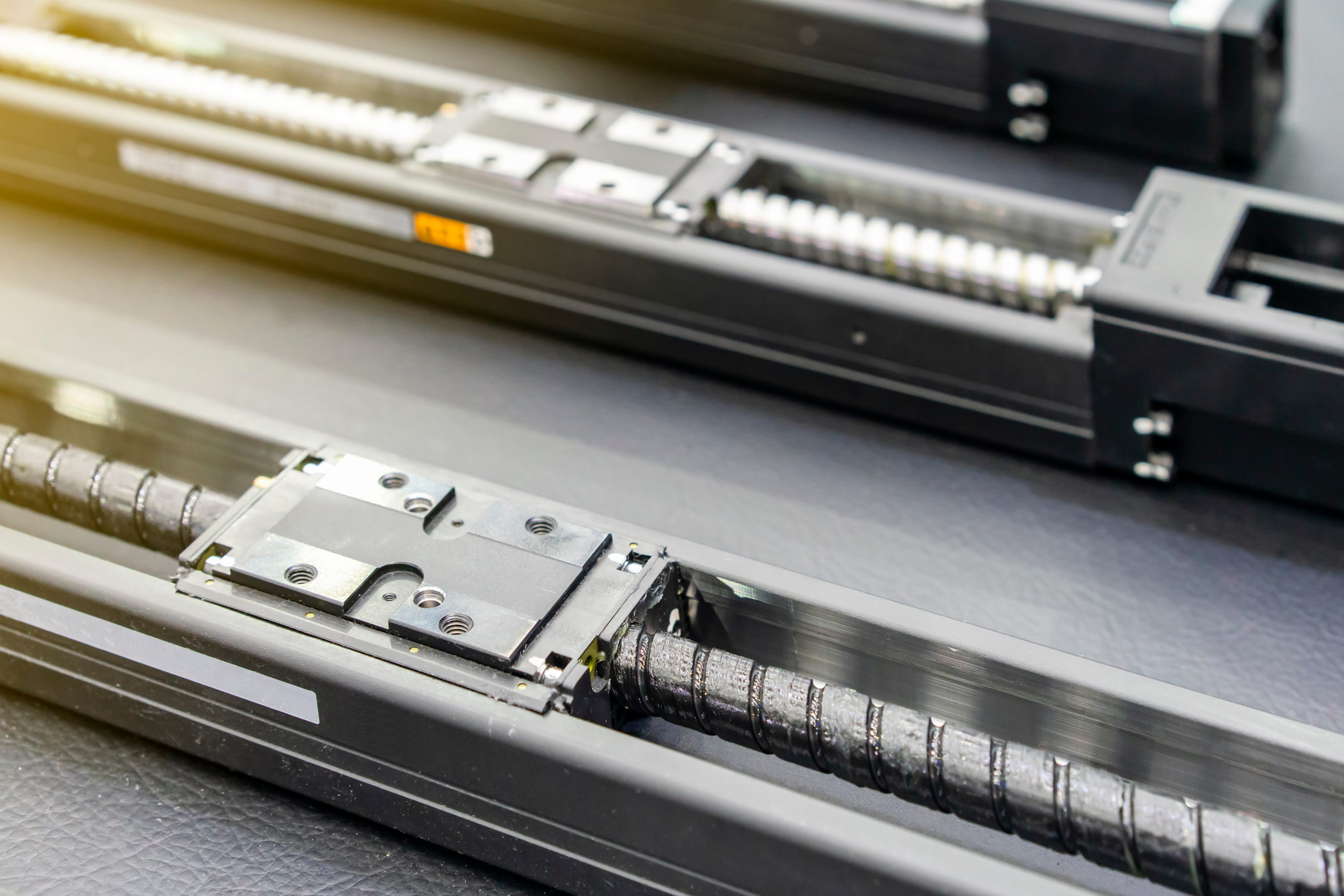
Frequently Asked Questions (FAQs)
Home » Resources » FAQs
PID tuning is a fundamental process in motion control systems, aiming to optimize the performance of feedback controllers. The acronym stands for Proportional-Integral-Derivative, representing the three key terms that shape the controller’s behavior. The proportional term responds to the current error, the integral term accumulates past errors, and the derivative term anticipates future errors. By adjusting these gains, engineers fine-tune the controller’s response to achieve stability, reduce overshoot, and minimize settling time.
Proportional (P): The proportional term responds to the current error by adjusting the control output proportionally. A higher P gain increases responsiveness but may lead to overshoot or instability.
Integral (I): The integral term accumulates past errors and helps eliminate steady-state error. It corrects for any long-term discrepancies between the desired and actual values.
Derivative (D): The derivative term anticipates future errors by considering the rate of change of the error. It dampens oscillations and improves stability.
Tuning a motor using the “Buzz” Method
Proportional (P): Increase the P gain until the system starts oscillating or “buzzing.” If there’s no oscillation, double the P gain.
Integral (I): Gradually increase the I gain until the steady-state error is minimized. Be cautious not to cause overshoot or instability.
Derivative (D): Add a small D gain to dampen oscillations and improve stability.
By adding pneumatic ports to your linear actuator, you can add positive pressure (5-10 psi) which aids in the protection of the internal components from outside contaminants. When air is added to the actuator, the internals will fill with air a build pressure, once the actuator is pressurized, air will want to escape; the air will escape where there are gaps or non-airtight areas, which is where the air will seep out. This controlled air seepage ensures that no contaminants can infiltrate the actuator at these vulnerable points.
Servo motors and stepper motors are both popular choices for motion control applications, but they operate differently and have distinct characteristics. Servo motors use feedback control systems to precisely control the position, speed, and torque of the motor shaft. They offer high accuracy, fast response times, and are well-suited for dynamic applications where precise positioning is crucial, such as robotics and CNC machines. In contrast, stepper motors move in discrete steps, with each step corresponding to a specific position. They are simpler to control and typically less expensive than servo motors but may lack the same level of accuracy and speed, making them more suitable for applications that don’t require high precision or rapid movement, such as 3D printers and automated equipment. The choice between servo and stepper motors depends on factors such as precision requirements, speed, cost, and the specific needs of the application.
A shunt regulator is a device that goes immediately after the power supply and is used to protect the power supply from back flow energy. If you have a vertical load and there is a power failure, the load will back drive and cause the motor to spin acting like a generator, this energy has to go somewhere and so goes up the line back to the power supply. This energy can cause the power supply to fail. When this occurs, a sensor inside the shunt will detect the voltage rise and will protect the power supply by turning on a resistor to ground where the energy can be safely dissipated to earth. Once the voltage level returns to normal, the voltage regulator will return the power supply to normal operations.
The National Sanitation Foundation (NSF) is a globally recognized organization dedicated to developing public health standards and certification programs for food, water, consumer products, and the environment. Their rigorous specifications ensure that products meet strict criteria for safety, quality, and sustainability, providing consumers and businesses alike with confidence in the products they use. From food safety to water treatment, NSF certification signifies adherence to industry-leading standards, promoting trust and reliability in the marketplace.
Deformations and Accuracy: Thermal-induced deformations can significantly impact the accuracy of motion systems. When a stage experiences temperature changes, its constituent materials expand or contract, altering the system’s dimensions. Even seemingly minor deviations can lead to positioning errors. Imagine a semiconductor wafer alignment system where nanometer-scale precision is essential. In such applications, thermal stability becomes critical. The system must maintain its precise positions over time, regardless of temperature fluctuations.
Nano-Scale Precision: Modern motion systems achieve remarkable precision—down to the nano-meter scale. At these levels, even the tiniest thermal effects matter. Consider a laser-based lithography system used in semiconductor manufacturing. The laser beam must hit specific points on the wafer surface with incredible accuracy. Any thermal expansion or contraction could misalign the pattern, affecting the final chip’s functionality.
Vacuum Environments: In ultra-high vacuum environments (common in semiconductor fabrication), heat dissipation becomes challenging. Traditional cooling methods (like air or liquid cooling) are often inadequate due to the vacuum conditions. Engineers must predict how the system will behave thermally during operation. This understanding helps select suitable components and design effective thermal management strategies.
Material Selection: Choosing the right materials is paramount. Materials with low coefficient of thermal expansion (CTE) are preferred. Granite is a popular choice for high-precision motion platforms. It provides excellent stability due to its minimal expansion or contraction with temperature changes. Other materials, such as ceramics or composites, are also used based on specific requirements. For example, silicon carbide (SiC) ceramics have low CTE and exceptional rigidity, making them suitable for certain applications.
Linear Encoders and Thermal Stability: Linear encoders play a crucial role in motion control. They provide accurate position feedback to the control system. High-precision linear encoders often use glass scales due to their exceptional thermal stability. Glass has an extremely low CTE, minimizing expansion effects. Some encoders incorporate compensation algorithms to correct for any remaining thermal expansion. These algorithms adjust the position feedback based on temperature variations.
In summary, understanding and managing thermal effects are essential for achieving precise, repeatable motion control. Whether integrated into granite or mounted on it, thoughtful design and effective thermal management strategies ensure minimal impact from temperature fluctuations on accuracy and repeatability.
IP (Ingress Protection) is the specification used for determining the level of protection something has against its environment.
Solids Water0 – No Rating for Protection0 – No Rating for Protection1 – Solid objects > 50mm1 – Vertical falling droplets2 – Solid objects > 12mm2 – Vertical falling droplets at 15 degrees3 – Solid objects > 2.5mm3 – Vertical falling droplets at 60 degrees4 – Solid objects > 1mm4 – Splashing water for 10 minutes5 – Partial protection against dust5 – Low pressure jets of water6 – Full protection against dust6 – Powerful Jets of water
Manufacturing Process:
Rolled Ball Screws: These are created by pushing uncut bar stock blanks through rotating tool dies in a single operation. The rolling process shapes both the internal and external threads of the lead screw and ball nut.
Ground Ball Screws: Ground screw threads are fabricated through an abrasion process. Material blanks rotate on their long axis between two machining centers, and extremely hard abrasive cutters carve out the threads from the cut blanks.
Strength and Precision:
Rolled Ball Screws: Generally possess more strength due to significant material strengthening achieved during the rolling process. However, they may not offer the same level of precision as ground ball screws.
Ground Ball Screws: Provide higher precision threading but are more expensive.
Cost and Application:
Rolled Ball Screws: More affordable than ground ball screws.
Ground Ball Screws: Cost more but offer superior precision.
– Rolled Ball-Screw: Cost-effective with decent repeatability, suitable for general automation.
– Ground Ball-Screw: Offers high precision and repeatability, ideal for applications requiring high accuracy.
– Rack and Pinion: Excellent for long strokes and high speeds, commonly used in heavy machinery.
– Acme Screw: Simple and low-cost, but with lower speed and repeatability, used in manual applications.
– Machine Screw: Similar to Acme screws but for lighter duties.
– Belt/Pulley: Great for long distances and high speeds, commonly found in conveyor systems.
– Linear Motor: Provides the highest speed and precision, but at a higher cost, used in high-speed automation.
DC Brush Actuators
Advantages:
– Simplicity: DC brush actuators are relatively simple in design and easy to control.
– Cost: Generally, they are less expensive to manufacture and purchase.
– Torque: They can provide high torque at low speeds.
– Controller: Simple and inexpensive controllers can be used.
Disadvantages:
– Maintenance: Brushes and commutators wear out over time, requiring regular maintenance and replacement.
– Efficiency: Lower efficiency compared to brushless motors due to friction losses.
– Noise: They generate more electrical and acoustic noise.
– Lifespan: Shorter lifespan due to wear and tear of brushes and commutators.
DC Brushless Actuators
Advantages:
– Efficiency: Higher efficiency due to the absence of friction losses from brushes.
– Maintenance: Minimal maintenance required as there are no brushes to wear out.
– Lifespan: Longer lifespan due to fewer moving parts.
– Performance: Better performance at higher speeds and more precise control.
– Noise: Lower electrical and acoustic noise.
Disadvantages:
– Cost: More expensive to manufacture and purchase.
– Complexity: Requires more complex electronic controllers.
– Initial Setup: More complicated to set up and integrate into systems.
Applications
– DC Brush Actuators: Often used in applications where cost is a significant factor and maintenance can be managed, such as in household appliances, automotive applications, and simple industrial machinery.
– DC Brushless Actuators: Preferred in applications requiring high efficiency, low maintenance, and precise control, such as in robotics, aerospace, medical devices, and high-performance industrial equipment.
Duty cycle is the percentage of time an actuator is active compared to the total time of one complete cycle. It’s crucial for ensuring the actuator doesn’t overheat and operates efficiently.
Steps to Calculate Duty Cycle:
1) Determine the Active Time:
Measure the time the actuator is running (active time).
2) Determine the Total Cycle Time:
This includes the active time plus the rest (inactive) time.
3) Calculate the Duty Cycle:
Duty Cycle (%)} = Active Time(s)/ Total Cycle Time(s) x 100
Example Calculation:
For example, if an actuator runs for 60 seconds and then rests for 40 seconds, the total cycle time is 100 seconds.
Active Time: 60 seconds
Rest Time: 40 seconds
Total Cycle Time: 60 + 40 = 100 seconds
Duty Cycle = 60%
Importance of Duty Cycle Calculations:
Prevents Overheating: Ensures the actuator has enough rest time to cool down.
Extends Lifespan: Reduces wear and tear by avoiding continuous operation.
Maintains Efficiency: Keeps the actuator operating within its optimal parameters.
Additional Considerations:
Load and Speed: Higher loads and speeds can affect the duty cycle. It’s essential to account for these factors to avoid overworking the actuator.
Environmental Conditions: Operating in non-ideal conditions (e.g., high temperatures) may require adjustments to the duty cycle.
By understanding and calculating the duty cycle, you can ensure your actuators perform reliably and efficiently over time.